The Integration of Six Core Components
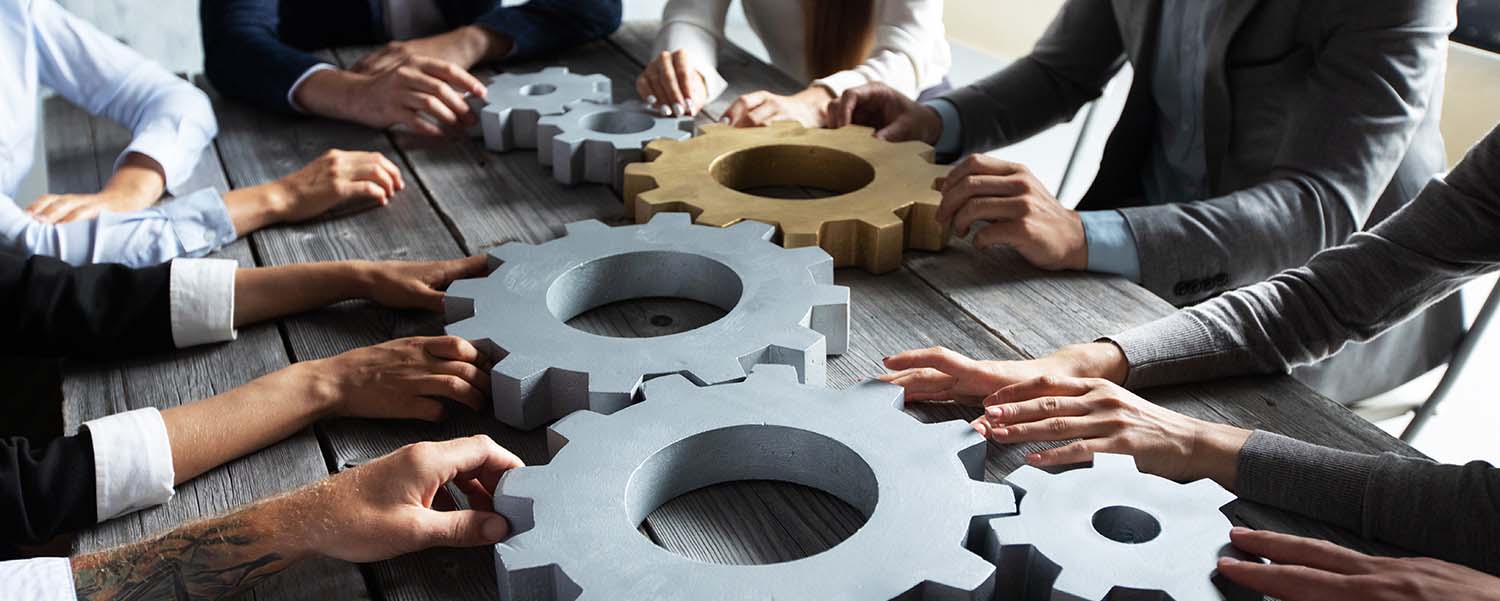
It is every individual’s responsibility to ensure cleaning and disinfecting of surfaces that are touched often (also called high-touch surfaces) are done effectively. This will decrease the risk of transmission of germs (bacteria, viruses, fungi, and protozoa) that cause infectious diseases.
The Centers for Disease Control and Prevention (CDC) has published a resource entitled Core Components of Environmental Cleaning and Disinfection. It focuses on cleaning and disinfection of noncritical surfaces in hospitals and, therefore, is applicable for surfaces in any facility.
The Global Biorisk Advisory Council® (GBAC) team at ISSA recommends following CDC’s six core components to help reduce the risk of spreading germs and infection from touching surfaces:
- Integrate cleaning and disinfecting surfaces into your facility’s safety culture.
- Educate and train all staff.
- Select appropriate cleaning and disinfection technologies and products.
- Standardize setting-specific cleaning and disinfection protocols.
- Monitor effectiveness and adherence to cleaning and disinfection protocols.
- Provide feedback on the adequacy and effectiveness of cleaning and disinfection.
While the GBAC team recognizes that this list of individual components is not necessarily new, the packaging of these six core components together as a formal guideline from CDC is. The COVID-19 pandemic has increased awareness of how germs can survive in the environment on surfaces, the need to read the disinfectant product label and the safety data sheet, and the dwell or wet contact time of the disinfectant on a surface. This is not just among the frontline cleaning industry but also among everyone who often touch the same surfaces.
The CDC six core components present a unique opportunity for all facilities to apply recent lessons learned from the COVID-19 pandemic and combine them with evidence-based practices and protocols to meet the elevated expectations of hygiene and cleanliness that is required to decrease the risk of being infected by any germ that can cause disease.
Let’s see how the CDC guideline provides descriptions and examples of activities in the Core Components.
Integrate
Integrate cleaning and disinfecting surfaces into your facility’s safety culture using program dashboards and policy documents that define and prioritize tasks, assign roles, and create schedules. This can be done by:
- Establishing a cleaning and disinfection program with a defined management structure and multidisciplinary participation and oversight.
- Holding regular meetings to review practices and quality measures and establish and review facility goals.
- Identifying and logging surfaces that are touched often, for example, by color-coding.
Educate and train
Educate and train all staff to be responsible for cleaning and disinfecting surfaces that are touched often by using a programmatic approach to in-person and virtual training. You can accomplish this by:
- Focusing education and training for cleaning and disinfection on:
- Learning/following cleaning and disinfection policies.
- Understanding the basic concepts of how you get sick and infectious disease transmission.
- Protecting themselves while working with the proper use of personal protective equipment (PPE), the safe use of chemicals and cleaning technologies, knowing infection control risks, and practicing worker safety as appropriate to the setting or situation.
- Training staff upon hire and at least annually. Keep records of training completion. If contracted services provide the training, make sure that it meets your requirements.
- Re-training to address weaknesses discovered during routine monitoring activities or audits.
- Holding competency-based training that accounts for staff turnover, education levels, language and cultural barriers, and multiple learning styles.
- Keeping a record of competency for all staff involved in cleaning and disinfection.
Select
Select appropriate cleaning and disinfection technologies and products to use based on function and safety metrics. To do this correctly, you must:
- Ensure that cleaning and disinfection technologies and products are tailored to the setting and standardized as much as possible.
- Use a systematic process to select technologies and products, including advanced technologies such as no-touch devices.
- Convene all stakeholders in the decision-making process for factors such as:
- Compatibility with device manufacturer’s instructions for use and safety data sheets.
- Dwell or wet contact time.
- Possible health risks.
- Effectiveness in disinfecting a surface.
- Impact on overall cleaning efficiency.
- Required expertise and training.
- Effect on surfaces or devices of repeated exposure to a product.
Standardize
Standardize setting-specific cleaning and disinfection protocols that are repeatable and measurable. This is possible to do by:
- Identifying standardized, setting-specific protocols for cleaning and disinfection, including the use of technologies and products.
- Emphasizing that high-touch surfaces must be cleaned effectively, accounting for differences in room layout, equipment, and risk.
- Clearly defining responsibilities for the cleaning and disinfection. Make sure that staff involved in cleaning and disinfection are aware of their responsibilities and are appropriately trained to fulfill them. Ensure that cleaning and disinfection supplies are easily accessible (e.g., cleaning carts are adequately stocked).
- Make sure that the protocols are readily available (e.g., posted online or available in hard copy) for review by staff.
- Include in the protocols appropriate PPE and facility-specific cleaning and disinfection technologies, products, and methods. Also, have processes for easy identification of equipment and rooms that have been properly cleaned and disinfected and are ready for use (e.g., tagging system, placement in the dedicated clean area).
- Establish the minimal cleaning time (MCT) for cleaning and disinfection for each room type or area. Define a process to establish MCTs, for example, by observing standardized cleaning protocols performed by experienced personnel. Align them with staffing plans to ensure that effective cleaning and disinfection can be completed and sustained. Disseminate MCTs so that others who are responsible for areas are aware of them. Enforce these times and empower staff to require adherence to them. Track cleaning times to identify factors that influence them and assess the need for mitigating those factors or revising the MCT.
Monitor effectiveness and adherence
Monitor effectiveness and adherence to cleaning and disinfection protocols and report on cleanliness performance using methods to validate cleaning. An environmental cleaning and disinfection monitoring strategy allows staff and the facility cleaning and disinfection program to understand the current state of facility cleanliness and identify improvement areas. Develop and implement a monitoring strategy for adherence to, and effectiveness of, cleaning and disinfection procedures. Include in the protocols for monitoring:
- Who should do the monitoring.
- What type of monitoring will be used (e.g., direct observation, fluorescent gel, adenosine triphosphate).
- How frequently the monitoring will occur.
- How monitoring data will be validated.
- Which rooms will be monitored.
- Which surfaces will be assessed.
Incorporate methods for monitoring cleaning adherence and effectiveness in addition to direct observation (e.g., fluorescent markers, ATP assays). Perform routine audits of adherence to cleaning and disinfection procedures.
Provide feedback
Provide feedback on adequacy and effectiveness of cleaning and disinfection to staff and stakeholders by routinely scheduling reviews to identify achievements and opportunities for improvement. You can do this by:
- Using monitoring data to improve facility cleaning and disinfection policies and procedures and safety.
- Presenting audit data to staff regarding their adherence to cleaning and disinfection procedures. Determine the best method to disseminate the information and foster shared accountability (i.e., all staff, management, and facility leadership take responsibility for consistent and successful adherence to protocols).
- Presenting audit data to leadership to identify active issues and strategies to mitigate these issues and validate the effectiveness of the overall cleaning strategy.
CDC states that, “No single blueprint exists for the best cleaning and disinfection method.” But CDC’s six Core Components are very closely aligned with the GBAC® STAR accreditation program to help establish and sustain a clean and healthy environment.
GBAC® STAR is a performance-based accreditation program that uses 20 Elements to help your facility demonstrate that you have the work practices, procedures, and protocols to instill confidence in your customers, staff, and key stakeholders that you are using appropriate cleaning, disinfection, and infectious disease prevention systems. The program was developed by the Global Biorisk Advisory Council (GBAC), a division of ISSA.