Aligning Automation Solutions
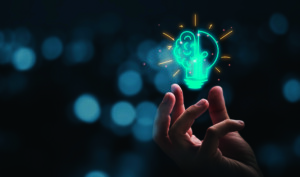
In today’s evolving cleaning industry, staying competitive relies on an organization’s ability to drive innovation and push the boundaries of traditional practices. Innovation may ignite fresh ideas, but the impact lies in implementing these ideas effectively, transforming challenges into opportunities, and enabling sustainable growth.
Aligning automated solutions with well-defined productivity goals is essential for facilities managers and cleaning service providers to achieve immediate efficiency gains and longer-term competitiveness.
Key expense categories
Let’s begin by discussing measuring cost savings and efficiency improvements by examining key expense categories typical in a cleaning company’s profit and loss statement. This approach helps highlight where automation solutions can align with and enhance custodial productivity goals. Cleaning businesses commonly manage four primary expense categories:
- Labor: Accounting for 50% to 65% of monthly costs, including wages, worker’s compensation, benefits, and employer taxes.
- Equipment: Covers essential cleaning machinery such as scrubbers, vacuums, and other tools.
- Consumables: Encompasses expendable supplies like chemicals and paper products.
- Overhead: Comprises fixed costs, such as rent, utilities, and administrative expenses.
Labor and equipment
This analysis will focus on labor and equipment, where automation can deliver the most significant cost savings. Automated solutions can reduce labor hours and optimize equipment usage, resulting in measurable impact by reducing expenses and increasing productivity. ISSA technician training divides cleaning into floor work, above-floor tasks, and bathrooms. We will focus on floor work using a vacuum.
When evaluating automation solutions for custodial productivity, it’s essential to consider how each type of vacuum impacts labor savings and efficiency.
Commercial corded vacuums offer low labor savings and limited productivity due to the time spent on cord management and manual operation.
Battery-powered vacuums improve productivity by allowing operators to move more freely. They deliver moderate labor savings in spaces that require agility.
Robotic vacuums operate independently, maximizing labor savings and productivity, allowing staff to focus on higher-priority tasks. Their hands-free functionality is particularly valuable in large or high-traffic spaces, where consistent, autonomous cleaning yields significant cost and labor benefits over time. Still, it is not a panacea for every situation.
A plan for automation
When investing in a robotic commercial cleaner, evaluate your unique cleaning requirements and workload to ensure automation aligns with expected productivity goals. Focus on data-driven insights for informed decision-making, ensuring readiness for the shift from manual to automated tasks. Seek out equipment that fits your tailored plan and select a vendor who offers long-term expertise and support, guiding support beyond the purchase for sustained operational success and measurable cost savings.
Following a deployment plan before the robots arrive on-site is essential for effectively measuring cost savings when aligning automation solutions with custodial productivity goals.
- Pre-deployment: This phase includes onboarding meetings with subject matter experts to clarify project goals, collect necessary operational data, and determine optimal deployment dates. This groundwork is crucial for defining how automation will fit into your unique cleaning workload and ensures your team is aligned with the upcoming transition.
- Deployment: During deployment, meticulous on-site preparation is vital, including mapping, editing, and customizing path configurations. Simulation runs allow teams to test the solution in real-life scenarios and sign off to ensure the robots meet pre-deployment requirements. Extensive training ensures the team understands how to operate and manage the robots. Detailed documentation, including instructions and troubleshooting tips, provides essential reference materials to keep everything running smoothly.
- Post-deployment engagement: Consistent customer support is crucial for sustained cost savings after deployment. A reliable provider should offer a help desk for quick issue resolution, remote troubleshooting for efficiency, access to a knowledge database for ongoing learning, and an analytics dashboard to monitor performance. Monthly review meetings enable your team to discuss performance, identify improvement areas, and make necessary adjustments.
- Ongoing service: Robust maintenance and technical support are essential to maximizing cost savings and efficiency in custodial automation. To maintain peak performance and extend the equipment’s lifecycle, begin with scheduled maintenance routines for both hardware and software. Regular firmware and software updates enhance functionality, security, and operational efficiency. Make sure spare parts are available for prompt repairs, minimizing downtime.
Choosing a reputable firm for your automation solution is essential, especially one familiar with robot hardware and software. Many operational issues are software-related, so a provider committed to regular, proactive engagement will help ensure optimal productivity, prevent downtime, and continually support your cost-saving objectives.
Embracing automation
Aligning automation solutions with custodial productivity goals can significantly enhance immediate and long-term efficiency. A structured approach–from assessing specific cleaning needs to selecting the right equipment, planning deployment, and securing ongoing support–is crucial to realizing the full benefits of automation. With a focus on labor and equipment savings, robotic vacuums and other automation solutions streamline workload, reduce manual tasks, and allow custodial teams to concentrate on higher-priority activities.
Partnering with a knowledgeable provider committed to proactive support can help organizations navigate challenges, minimize downtime, and achieve consistent results. Well-thought-through deployment, training, and maintenance strategies ensure that automation aligns with the company’s productivity goals, resulting in measurable cost savings and operational improvements.
Embracing these technologies drives cost efficiency and positions custodial operations to meet evolving industry standards, securing a competitive advantage in today’s dynamic cleaning landscape. With the right strategy and support, automation becomes an asset that transforms traditional custodial operations into highly efficient, data-driven systems.
“Innovation is the ability to see change as an opportunity, not a threat.” –Steve Jobs.
Jon Hill is the CEO of Cobotiq. He provides business managers with information on creating and implementing profitability. He is also a frequent speaker and presenter on the future impact of automation and technology in the cleaning industry.
Sidebar
Financial Clarity in Workloading Strategies
Profit & Loss and Balance Sheet Insights for Calculating Productivity